Introduction: Importance of Rare Earth Elements Recycling
Rare earth elements (REE) are essential elements for modern technologies such as smartphones, electric car batteries, and wind turbines. This is because they are used in a variety of industries, from electronics to renewable energy. However, rare earths are not widely distributed on Earth, and China accounts for about 70% of global production.
As China restricts rare earth exports, supply has decreased, leading to supply chain instability and price volatility. Rare earth elements recycling is a crucial solution to address this supply challenge and ensure a stable supply of these critical materials. Through rare earth elements recycling from various sources like waste, coal ash, and end-of-life products, we can reduce our reliance on finite raw materials and mitigate environmental impacts.
Rare earth elements recycling technologies are being actively developed and optimized for higher efficiency and lower environmental burden, making rare earth elements recycling a key enabler for a sustainable and resilient future.
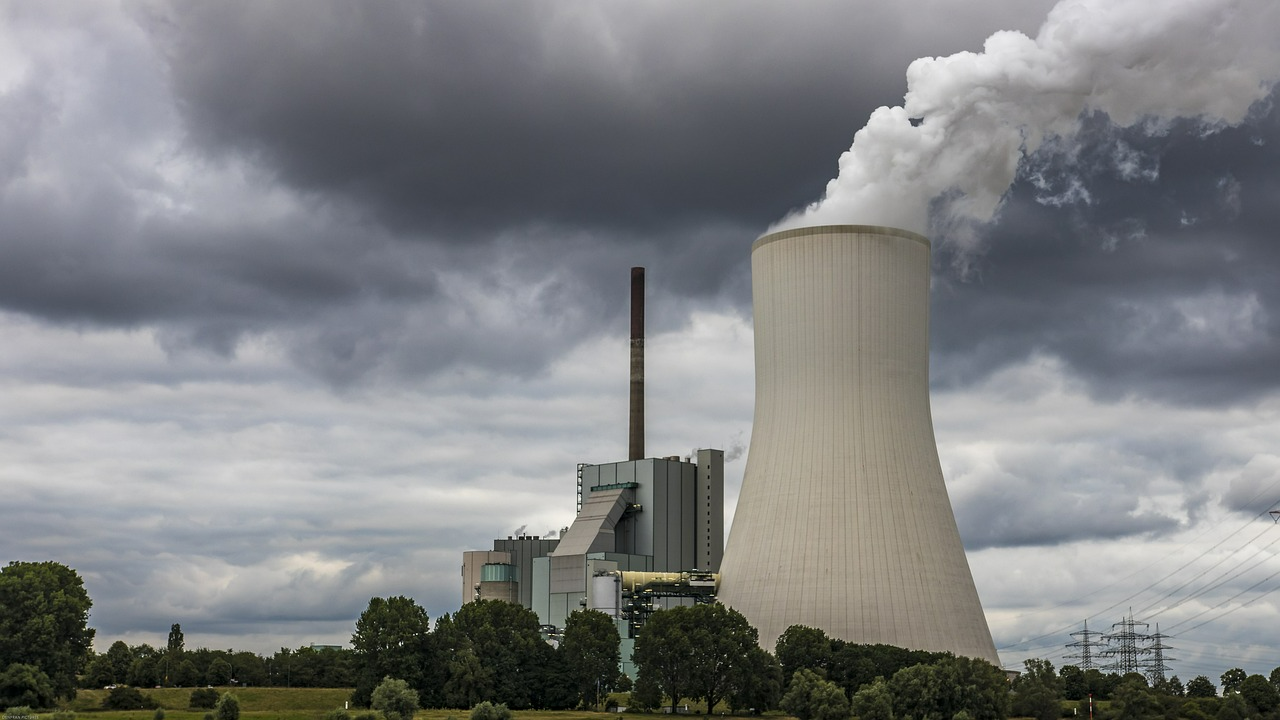
Type of Rare Earth Elements and Applications
Type | Element | Symbol | Number | Application | ||||||||
LightREE(Rare Earth Element) | Lanthanum | La | 57 | Catalyst, Electrode, Hydrogen storage, Optical glass, Laser | ||||||||
Cerium | Ce | 58 | Chemical oxidizers, Glass, Ceramic coloring agent | |||||||||
Praseodymium | Pr | 59 | Magnet, Laser, Glass, Ceramic coloring agent | |||||||||
Neodymium | Nd | 60 | Magnet, Laser, Ceramic condenser | |||||||||
Promethium | Pm | 61 | Navigation lighting, Nuclear battery, Luminescent paint | |||||||||
Samarium | Sm | 62 | Magnet, Laser, Neutron control rod | |||||||||
Europium | Eu | 63 | Phosphors, Laser, Mercury lamps, Nuclear magnetic resonance relaxant | |||||||||
HeavyREE(Rare Earth Element) | Gadolinium | Gd | 64 | Neutron absorbing material, Iron-chromium alloy | ||||||||
Terbium | Tb | 65 | Green phosphor, Laser, Ultrasonic detection system | |||||||||
Dysprosium | Dy | 66 | Magnet, Laser, Illumination light source | |||||||||
Holmium | Ho | 67 | Magnet, Optical fiber, Communication devices | |||||||||
Erbium | Er | 68 | Military, Infrared laser, Vanadium steel, Optical fiber | |||||||||
Thulium | Tm | 69 | Portable X-ray, Laser, Metal halide lamp | |||||||||
Ytterbium | Yb | 70 | Infrared laser, Optical fiber amplifier, Nuclear medicine | |||||||||
Ruthenium | Lu | 71 | Battery, Light emitting diode(LED), Radiation equipment | |||||||||
Scandium | Sc | 21 | Lightweight aluminum and scandium alloy for aerospace | |||||||||
Yttrium | Y | 39 | Phosphor, Microwave filter, Superconductor, Chemotherapy |
Demand for rare earths is surging due to the growth of the green industry. According to the International Energy Agency (IEA), global demand for rare earths is expected to increase 3-7 times by 2040, driven by the expansion of electric vehicles and wind power by 2050.
In response, efforts are needed to secure a stable supply of rare earths, and rare earth recycling technology is being highlighted as a key technology for securing sustainability and stability. Development of rare earth recycling technologies is actively underway around the world, and it is expected that once these technologies are completed, they will contribute to securing a stable supply of rare earths and reducing environmental pollution.
U.S. Develops Rare Earth Elements Recycling (Extraction) from Waste
American Resources Corporation (ARC), a Nasdaq-listed company, plans to build a rare earth purification and separation facility in Noblesville, Indiana. ARC’s wholly owned subsidiary, ReElement Technologies LLC, is a leading supplier of high-performance refining capacity for batteries and rare earth elements, and is targeting completion of the first commercial rare earth purification and separation facility in the United States by 2025.
ARC’s rare earth purification and separation facility will be based on the “ligand-exchange substitution (LAD) chromatography” technology developed by Purdue University. LAD chromatography is an environmentally friendly and efficient rare earth purification technology that could enable the United States to perform the final stage of rare earth processing, which had previously been reliant on China.
In 2019, the Ames Laboratory, a U.S. Department of Energy national laboratory, developed a selective rare earth extraction technology that uses copper as a capture metal from aqueous solutions. This technology has the advantage of being less environmentally burdensome as it does not use acids.
Japan Develops Rare Earth Elements Recycling without Magnet Disassembly
Nissan has announced the development of a new rare earth elements recycling technology that can recover 98% of rare earths from electric vehicle motor magnets. The conventional technology requires the magnet to be disassembled, which is time-consuming and expensive. The new technology can recover rare earths without disassembling the magnet, making it more efficient and economical.
The new technology uses a melting furnace to heat the magnet, carbon processing material, and cast iron together. The heated mixture is heated to 1,400 degrees Celsius, at which point the rare earth elements oxidize . The oxidized rare earths are then melted using a borosilicate-based solvent, and the melted oxide layer, called slag, floats to the top. The iron-carbon alloy layer, which is denser, sinks to the bottom, making it easy to recover the rare earths.
Nissan plans to commercialize the technology by 2025. When commercialized, it is expected to help reduce the use of rare earths in electric vehicles and diversify the rare earth supply chain. Tokyo University and Hitachi have been conducting pilot studies on rare earth extraction and rare earth metal manufacturing technology using capture metals and vacuum distillation since 2017. This technology has the advantage of being less environmentally burdensome as it does not use acids.
In 2018, they developed a method for extracting and separating elements from dry permanent magnets using magnesium chloride. This technology has the advantage of being able to extract rare earths without disassembling permanent magnets, which can increase recovery rates.
Currently, Tokyo University and Hitachi are developing rare earth selective recovery technology using selective chlorination. This technology is expected to improve recovery rates and efficiency by selectively recovering rare earths using the chemical properties of rare earth elements.
South Korea Develops Rare Earth Elements Recycling (Extraction) from Coal Ash and End-of-Life Permanent Magnets
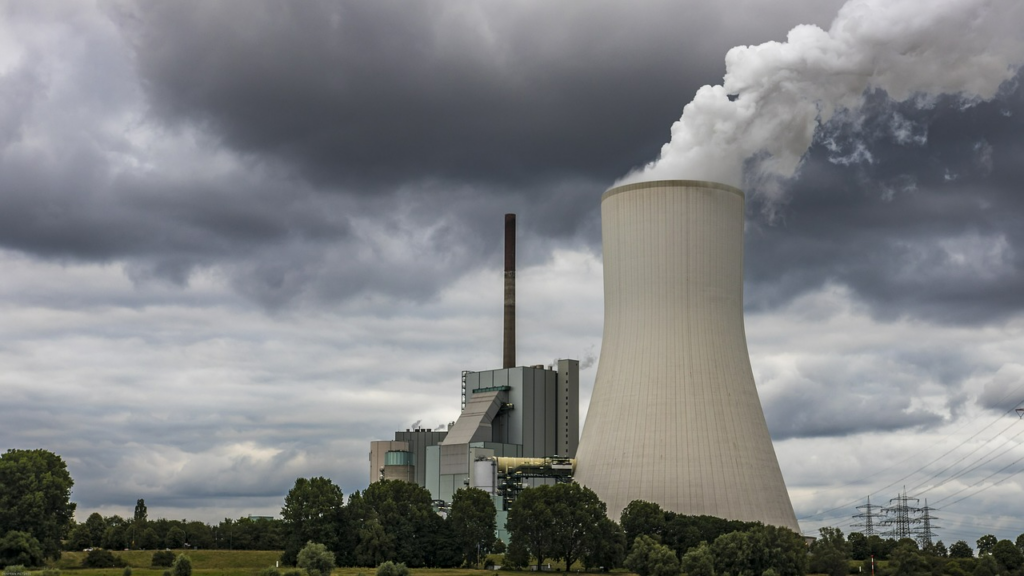
Gangwon Province, South Korea, has been exploring various low-carbon, environmentally friendly industries using carbon mineralization technology in collaboration with the Korea Institute of Geoscience and Mineral Resources (KIGAM) and Kangwon National University. In particular, the province has recognized that the production of rare earths from coal ash generated by coal-fired power plants in the province is a core technology for both climate change adaptation through greenhouse gas reduction and securing critical minerals domestically to enhance industrial competitiveness.
Gangwon Province is currently implementing a five-year, 110 billion won (approximately $90 million) project to establish a rare earth mini-pilot plant. The project is to demonstrate the technology for producing rare earths using coal ash from coal-fired power plants located in Gangwon Province. Through the rare earth mini-pilot plant project, Gangwon Province plans to verify the stability and economic feasibility of rare earth extraction technologies and then proceed with full-scale projects based on the results. It is expected that the successful commercialization of rare earth recycling technologies will contribute to the revitalization of the province’s manufacturing industry in the materials sector and the promotion of the local economy.
On August 3, 2023, Sunglim Rare Metals, a research institute company jointly established by Sunglim Advanced Industries, the only permanent magnet manufacturer in Korea, and KIGAM, announced that it had completed the demonstration of a recycling process for end-of-life permanent magnets.
Sunglim Rare Metals was established in 2015 with the support of the Global Top Environmental Technology Development Project and has been developing a technology to recover rare earths from end-of-life permanent magnets. The process demonstrated this time is a traditional wet-based process that involves crushing end-of-life permanent magnets to create a leaching solution and selectively leaching and separating the rare earths.
Sunglim Rare Metals succeeded in recovering more than 90% of rare earths from end-of-life permanent magnets through this demonstration. In addition, the recovered rare earths can be refined to a high purity, which is highly valued for recycling. Sunglim Rare Metals plans to build a commercial plant by 2025 based on the results of this demonstration. It is expected that the commercial plant will be able to recycle more than 1,000 tons of rare earths per year upon completion.
Conclusion : Rare Earth Elements recycling
As the world grapples with the challenges of meeting skyrocketing rare earth demands while mitigating environmental impacts, rare earth elements recycling these critical elements has emerged as a game-changing solution. Through innovative technologies that enhance recovery rates, reduce environmental burdens, and enable domestic production capabilities, rare earth elements recycling presents a multifaceted approach to achieving a sustainable and resilient future.
By prioritizing research, development, and large-scale implementation of advanced rare earth elements recycling methods across industries and nations, we can pave the way for a circular economy that maximizes resource efficiency and reduces our reliance on finite raw materials. Collaborative efforts between governments, industries, and research institutions will be crucial in driving this transition, fostering knowledge sharing, and scaling up rare earth elements recycling infrastructure globally.
Ultimately, the widespread adoption of rare earth elements recycling technologies will not only secure a stable supply of these vital elements but also contribute to reducing greenhouse gas emissions, minimizing waste, and promoting sustainable practices across the entire supply chain. As we strive towards a greener, more equitable future, rare earth elements recycling stands as a pivotal catalyst for achieving our sustainability goals while fueling economic growth and technological innovation.
※ This report has been compiled for the purpose of providing general information. It is based on data gathered by CHEMiFORGE. Should you have any inquiries or need to make decisions based on this report, it is advisable to consult with a CHEMiFORGE.