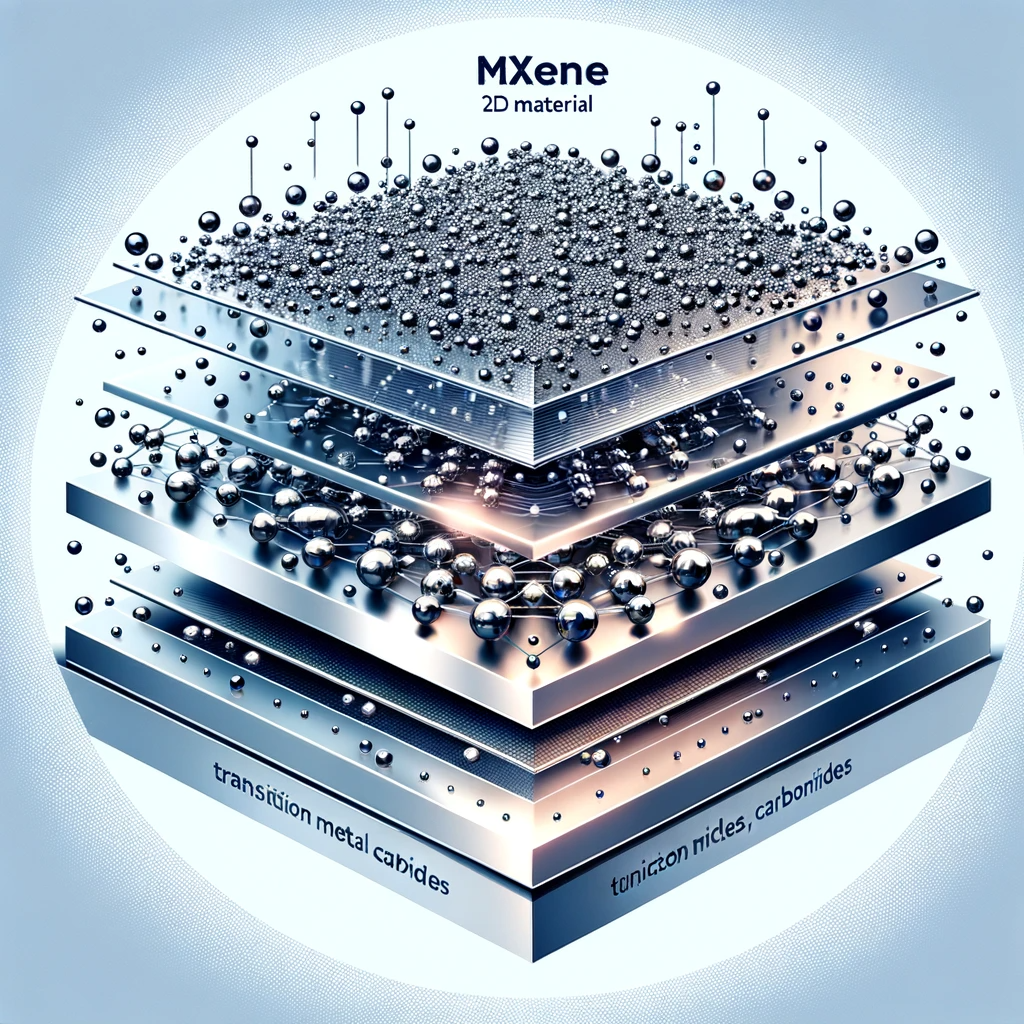
[Dall-E]
Introduction: MXene Synthesis
MXenes, a family of two-dimensional materials, have garnered significant attention due to their unique properties and potential applications in various fields. Among these, Ti3C2Tx MXene stands out for its exceptional electrical conductivity, hydrophilicity, and mechanical strength. This paper presents a detailed, step-by-step guide for the synthesis and delamination of MXene, offering valuable insights for researchers and industry professionals.
Unveiling the Revolutionary World of MXene Synthesis
Mxene synthesis involves the selective etching of specific layers from parent MAX phases, which are layered ternary carbides or nitrides. The resulting 2D materials, known as MXenes, possess a unique combination of metallic conductivity, hydrophilic surfaces, and tailorable properties, making them attractive for various applications, including energy storage, catalysis, and environmental remediation.
The mxene synthesis process typically begins with the selection of a suitable MAX phase precursor. These precursors are composed of early transition metals (M), carbon or nitrogen (X), and an A-group element, such as aluminum or silicon. Through controlled etching, the A-group layers are selectively removed, exposing the MXene sheets with a unique surface termination.
One of the most widely employed mxene synthesis methods is the chemical exfoliation route, which involves the use of etchants like hydrofluoric acid (HF) or a mixture of hydrochloric acid (HCl) and lithium fluoride (LiF). This approach has proven effective in producing high-quality MXenes, but it also raises concerns about the handling and disposal of hazardous reagents.
To address these challenges, researchers have explored alternative mxene synthesis techniques, such as electrochemical exfoliation, molten salt synthesis, and the use of ionic liquids. These methods aim to reduce the environmental impact and improve the scalability and cost-effectiveness of MXene production.
Mxene synthesis is not without its challenges. Controlling the etching process to achieve uniform and reproducible MXene sheets is crucial for their practical applications. Additionally, understanding the role of surface terminations and their impact on the properties of MXenes is an active area of research.
Furthermore, the development of large-scale mxene synthesis methods is essential for transitioning from laboratory-scale production to industrial-scale manufacturing. Efforts are underway to explore continuous flow synthesis, scalable electrochemical exfoliation, and other high-throughput techniques to meet the growing demand for MXenes.
As the field of mxene synthesis continues to evolve, interdisciplinary collaborations between materials scientists, chemists, and engineers will be crucial in overcoming the existing challenges and unlocking the full potential of these remarkable 2D materials. With continued research and innovation, mxene synthesis could pave the way for groundbreaking applications in energy storage, catalysis, sensing, and beyond.
Synthesis of MXene
- Selection of MAX Phase Precursor: MAX phases are layered, hexagonal carbides or nitrides, where ‘M’ is an early transition metal, ‘A’ is an A-group element (mostly 13 and 14), and ‘X’ is either carbon or nitrogen. For MXene, Ti3AlC2 is commonly used. The process begins with the selection of an appropriate MAX phase precursor. The precursor powder mixture for a MAX synthesis is usually dry mixed for a few hours to 24 h or more in air, followed by reactive sintering at 1350~1400 °C under a controlled environment. The unique layered structure of the MAX phase is pivotal for the successful synthesis of MXene.
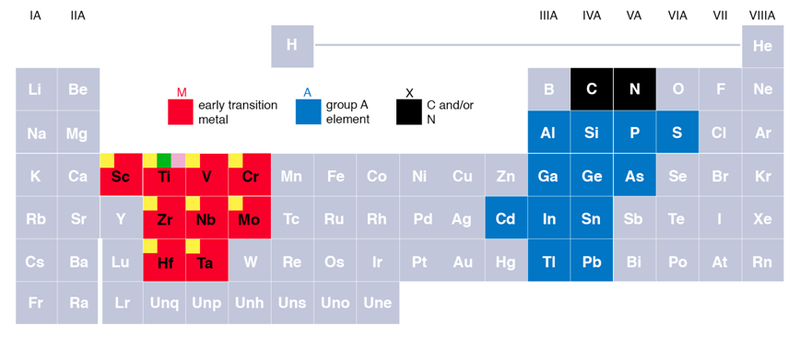
https://en.wikipedia.org/wiki/MAX_phases
- Etching Process: The most used method is HF-etching, either pure HF, mixed HF with other acids or HF formation via a fluoride salt such as lithium fluoride(LiF) mixed with HCl. This step is crucial for removing the aluminum layers from Ti3AlC2, leading to the formation of accordion-like structures of Ti3C2Tx. Before etching, the MAX phase material is often ground into a fine powder. This increases the surface area, allowing for more efficient etching. The particle size of the MAX phase can influence the etching process and the quality of the MXene produced. The concentration of the etching solution, temperature, and duration of etching are crucial. Over-etching can damage the layers, while under-etching may leave residual ‘A’ elements.
- Washing and Centrifugation: After etching, the material is thoroughly washed with deionized water. This step is crucial to remove residual acid and byproducts from the etching process. The washing process might be repeated several times to ensure thorough cleaning. Centrifugation is then used to separate the etched product. The speed and duration of centrifugation can affect the yield and quality of the MXene layers.
- Delamination: The multilayered Ti3C2Tx obtained from etching is then subjected to delamination to separate individual layers. This is achieved through intercalation, where organic molecules like dimethyl sulfoxide (DMSO) are inserted between the MXene layers. After intercalation, additional washing with water causes the intercalated layers to swell and separate, leading to the exfoliation of individual MXene sheets. The choice of intercalation agent and its concentration play a significant role in the successful delamination of MXene layers.
- Drying: The final step involves drying the delaminated MXene. The drying method (such as vacuum drying, freeze-drying, or air drying) can significantly impact the properties of the final product. For instance, vacuum drying can preserve the layered structure, while freeze-drying can lead to a more porous structure. Different drying methods, like vacuum drying, can be used depending on the desired morphology and application.
Conclusion
As the field of mxene synthesis continues to evolve, interdisciplinary collaborations between materials scientists, chemists, and engineers will be crucial in overcoming the existing challenges and unlocking the full potential of these remarkable 2D materials. With continued research and innovation, mxene synthesis could pave the way for groundbreaking applications in energy storage, catalysis, sensing, and beyond.
The MXene obtained through mxene synthesis is characterized using various techniques like X-ray diffraction, scanning electron microscopy, and transmission electron microscopy to confirm its structure and properties. This MXene from mxene synthesis finds applications in energy storage, electromagnetic interference shielding, environmental remediation, and as sensors due to its high conductivity, flexibility, and hydrophilic nature. Optimizing the mxene synthesis process and exploring new synthesis routes will be vital to producing high-quality MXenes with tailored properties for diverse practical applications.
※ This report has been compiled for the purpose of providing general information. It is based on data gathered by CHEMiFORGE. Should you have any inquiries or need to make decisions based on this report, it is advisable to consult with a CHEMiFORGE.