Lignin, a complex and abundant polymer found in plant cell walls, is emerging as a promising sustainable alternative to non-renewable resources. As the world strives for a more environmentally-friendly future, innovative solutions like the Lignin process are gaining attention for their potential to harness the power of lignin, replacing petroleum-based plastics and other materials. This remarkable natural polymer holds immense potential to revolutionize various industries and contribute to a more sustainable future.
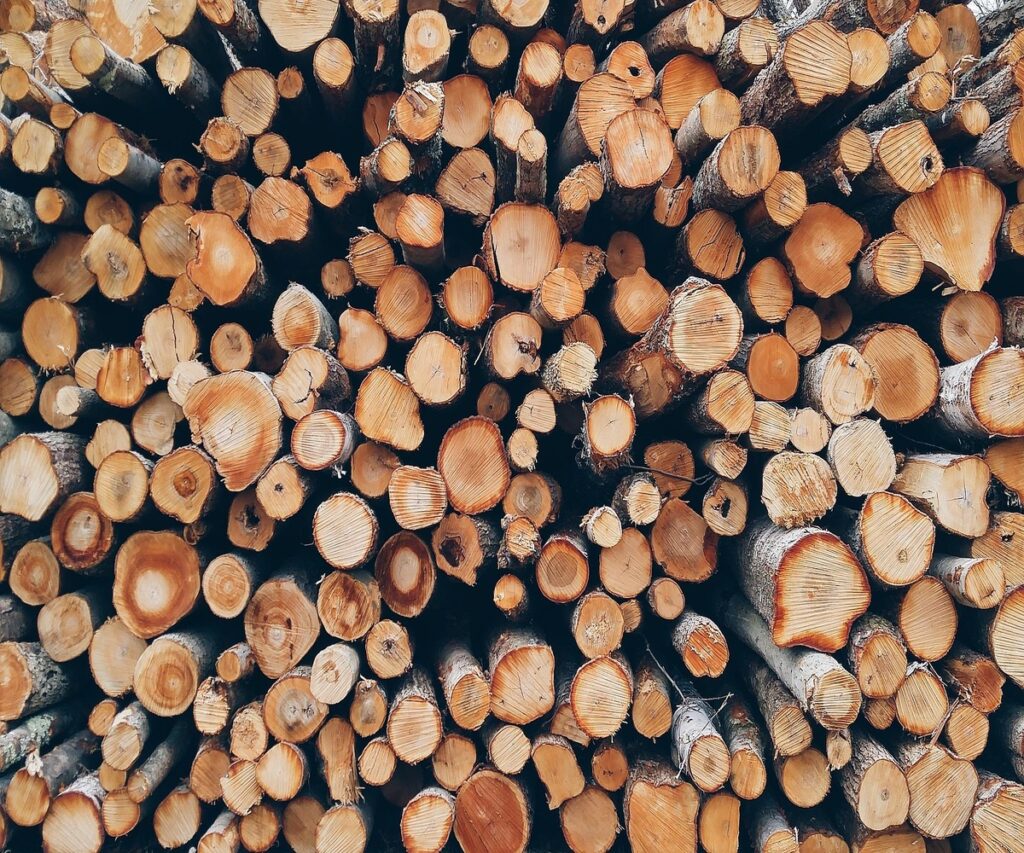
The Evolution of Lignin: From Waste to Valuable Resource
For years, lignin was treated as a mere waste by-product in the pulp and paper industry, often discarded or burned as fuel during the paper production. However, this perception has undergone a significant shift as researchers and scientists delved deeper into understanding the unique properties and immense value of this renewable resource. It is now recognized as a treasure trove of opportunities, awaiting exploration and exploitation for the greater good of humanity and the planet.
Unlocking Potential of Lignin Process
Driven by the need for sustainable solutions, scientists have developed the innovative Lignin process to harness the power of lignin. This efficient Lignin process, developed by researchers, extracts lignin from the by-products of pulp manufacturing, enabling its utilization in the production of polyurethane foams, adhesives, and coatings to its full potential.
The Lignin process represents a significant stride towards a circular economy, transforming what was once considered waste into a valuable resource. This remarkable process has the potential to revolutionize various industries by harnessing the power of lignin. The Lignin process can be utilized repeatedly, ensuring its sustainable impact is amplified manifold. Researchers at prestigious institutions have also made significant contributions to the field of lignin-recovery and modification, further enhancing the potential of the Lignin process.
A certain professor has developed an efficient method for lignin recovery, leveraging its unique chemical properties and separating it from other constituents. This innovative approach paves the way for large-scale production and widespread adoption of lignin-based materials through the Lignin process. The Lignin process can then be applied to these recovered lignin materials, expanding their applications across diverse sectors.
Moreover, another professor has focused on the chemical conversion of lignin’s molecular structure, enhancing its strength, usability, and imparting valuable properties such as antibacterial and antioxidant characteristics, as well as high hygroscopicity. These modifications open up a new realm of possibilities for the Lignin process, allowing it to be used in the creation of advanced materials with tailored properties. The Lignin process can then be employed to incorporate these modified lignin compounds into various products, ensuring their versatility in various industries.
This innovative approach paves the way for large-scale production and widespread adoption of lignin-based materials. Meanwhile, another professor has focused on the chemical conversion of lignin’s molecular structure, enhancing its strength, usability, and imparting valuable properties such as antibacterial and antioxidant characteristics, as well as high hygroscopicity. These modifications open up a new realm of possibilities for lignin, expanding its applications and ensuring its versatility in various industries.
https://pubs.rsc.org/en/content/articlehtml/2024/gc/d3gc04299e
Lignin: A Sustainable Solution for Plastics
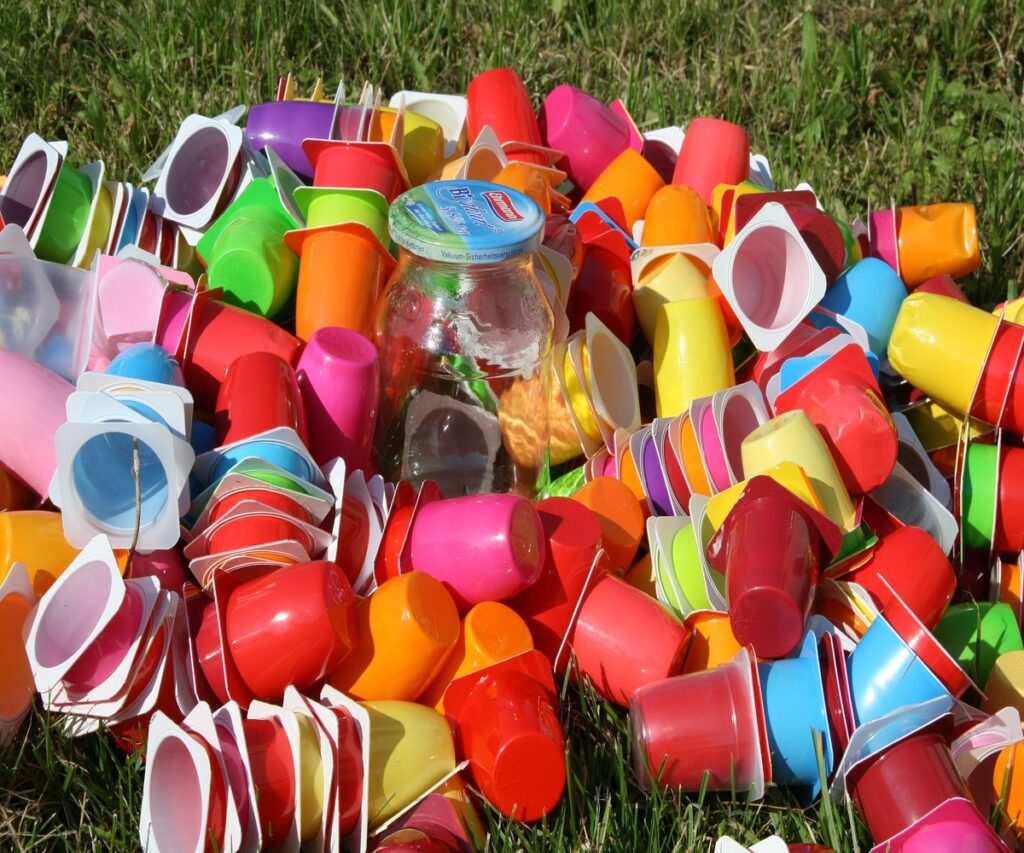
One of the most promising and impactful applications of lignin lies in the development of sustainable plastics. Petroleum-based plastics have long been a significant contributor to pollution and climate change, creating an urgent need for eco-friendly alternatives. Lignin, derived from renewable resources, has the potential to serve as a raw material for the production of bio-based plastics that are biodegradable and significantly reduce the environmental impact associated with traditional plastics. The use of these sustainable alternatives in plastics could revolutionize the plastics industry, providing a solution to the growing problem of plastic waste and its detrimental effects on the environment.
Remarkably, these bio-based plastics exhibit properties comparable to their petroleum-based counterparts, including mechanical strength, thermal stability, and barrier properties. This makes them a viable alternative for a wide range of applications, from packaging to construction, without compromising on performance or quality. The development of sustainable plastics has the potential to replace conventional plastics in numerous industries, offering an environmentally-friendly option that meets the same stringent requirements as traditional plastics. Furthermore, the biodegradable nature of these sustainable plastics could significantly reduce the amount of plastic waste accumulating in landfills and oceans, mitigating the negative impact on ecosystems and marine life.
Beyond the environmental benefits, the use of lignin in plastics could also provide economic advantages. As a renewable resource derived from plant biomass, lignin is abundant and cost-effective, potentially reducing the overall production costs of bio-based plastics. Additionally, the development of lignin-based plastics could create new opportunities for the forestry and agricultural industries, as they could become suppliers of the raw materials needed for its extraction. This could lead to increased revenue streams and sustainable practices within these industries.
Moreover, the versatility of bio-based plastics opens up new avenues for innovation and product development. Researchers and manufacturers can explore different blends and formulations to create specialized plastics tailored to specific applications, such as high-performance packaging, biodegradable construction materials, or advanced medical devices. This versatility could drive the development of new and improved products, foster technological advancements, and create new market opportunities.
Overall, the development of sustainable plastics represents a significant step towards a more sustainable future. By harnessing the potential of abundant and renewable resources like lignin, we can reduce our reliance on non-renewable resources, mitigate environmental pollution, and create a circular economy that prioritizes sustainability and resource efficiency.
Expanding Applications of Lignin
Beyond plastics, lignin offers a diverse array of applications, demonstrating its versatility and potential to transform multiple industries. It can serve as a feedstock for the production of renewable chemicals like phenol and vanillin, both of which have numerous applications in industries such as pharmaceuticals, cosmetics, and food additives.
Moreover, lignin can be utilized directly as a biofuel or processed into a liquid fuel, contributing to the development of sustainable energy sources and reducing reliance on fossil fuels. This versatility positions lignin as a key player in the transition towards a more sustainable and circular economy.
Challenges and Future Prospects of Lignin
While the potential of lignin is undeniable, several challenges must be addressed to fully develop and commercialize lignin-based materials. One of the major obstacles is the heterogeneity of lignin, which can vary depending on the source and extraction method. This heterogeneity makes it difficult to control and predict the properties and behavior of lignin-based materials, posing a challenge for large-scale production and standardization.
To overcome this challenge, it is crucial to establish robust standardization protocols and quality control measures, ensuring consistency and reliability in the production of lignin-based products. Furthermore, ongoing research is needed to optimize lignin-recovery and treatment methods, aiming to reduce costs and enhance efficiency. By addressing these challenges, the widespread adoption of lignin as a sustainable resource will become more feasible, reducing reliance on non-renewable resources and minimizing the environmental impact of industrial processes.
The development of lignin-based materials through the Lignin process and the forestry industry holds the potential to create a virtuous cycle of sustainability and economic growth. The Lignin process can be applied to the by-products of the forestry industry, extracting and utilizing lignin for various applications. This not only reduces waste but also creates value-added products through the Lignin process.
The Lignin process can be employed to produce sustainable plastics from lignin, contributing to a circular economy. Additionally, the Lignin process can be used to derive renewable chemicals and biofuels from lignin, reducing reliance on fossil fuels. The Lignin process is versatile and can be adapted to different feedstocks, making it a valuable tool for the forestry industry.
In conclusion, lignin stands as a remarkable renewable resource with vast potential for various applications, including the production of sustainable plastics, renewable chemicals, and biofuels through the Lignin process. By addressing the challenges related to lignin’s heterogeneity, standardization, and cost-efficiency, the Lignin process can be optimized, and lignin can play a pivotal role in promoting sustainability, reducing environmental impact, and providing economic benefits to industries such as forestry. The Lignin process can be continuously improved and refined, ensuring its widespread adoption and maximizing its impact on sustainability efforts.
※ This report has been compiled for the purpose of providing general information. It is based on data gathered by CHEMiFORGE. Should you have any inquiries or need to make decisions based on this report, it is advisable to consult with a CHEMiFORGE.