Introduction: Hydrogen Direct Reduction for Iron Process
The global steel industry stands at a crossroads, facing the imperative to reduce its substantial carbon footprint amid escalating concerns over climate change. Traditional ironmaking processes, heavily reliant on coking coal and blast furnaces, are among the largest industrial sources of CO2 emissions. This context propels the search for alternative, sustainable methods of iron production. Hydrogen Direct Reduction (HyDR) of iron emerges as a compelling solution, offering a pathway to decarbonize steel production by leveraging hydrogen as a reducing agent.
Hydrogen Direct Reduction represents a transformative approach where hydrogen gas is used to reduce iron oxides (typically in the form of pellets or fines) directly to metallic iron at elevated temperatures, bypassing the carbon-intensive blast furnace route. This process not only promises a significant reduction in CO2 emissions but also aligns with the global shift towards green energy, especially when the hydrogen used is sourced from renewable energy through water electrolysis.
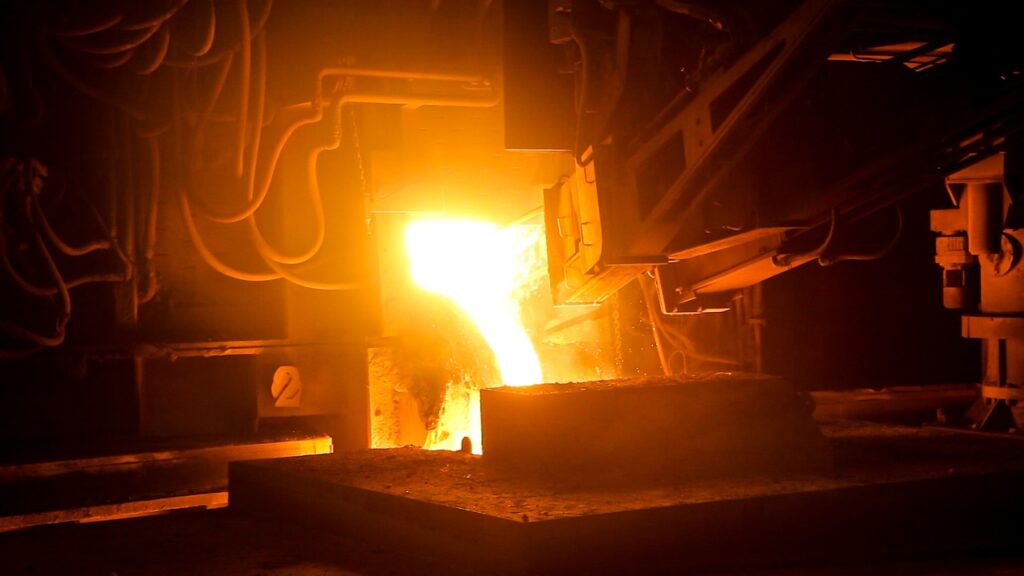
Understanding of Hydrogen Direct Reduction (HyDR)
The principle underlying Hydrogen Direct Reduction (HyDR) is the reaction of hydrogen with iron oxides, removing oxygen to produce water vapor and pure iron. This reaction occurs in several steps, starting from the reduction of hematite (Fe2O3) to magnetite (Fe3O4), followed by the conversion of magnetite to wüstite (FeO), and finally, the reduction of wüstite to iron (Fe). Each of these reduction steps is influenced by factors such as temperature, pressure, and the physical characteristics of the iron ore, making the optimization of HyDR conditions a subject of intensive research.
Investigating the Effects of Pre-Oxidation on Hydrogen Direct Reduction of Iron Powders
In a recent study, investigations into hydrogen direct reduction (HyDR) of iron focused on analyzing the complex behavior of iron powder burned under different conditions. Central to the experimental approach were methods designed to capture the kinetics of reduction, phase transitions, and the microstructural evolution of iron throughout the process.
Iron oxide powder, resulting from the combustion of pure iron powder, was examined in two states: as-combusted (PartOx) and pre-oxidized (FullOx). FullOx was achieved by subjecting PartOx to additional oxidation, ensuring a complete transition to hematite.
Conducted to measure the reduction kinetics, the TGA (Thermogravimetric Analysis) experiments involved exposing PartOx and FullOx samples to pure hydrogen at varying temperatures (400°C, 450°C, and 500°C). This method allowed for the real-time tracking of mass loss, directly correlating to the extent of reduction. And, a suite of techniques, including scanning electron microscopy (SEM) with energy dispersive spectroscopy (EDS) and electron backscatter diffraction (EBSD), alongside ex-situ and in-situ high-energy X-ray diffraction (HEXRD), provided detailed insights into the phase distribution and microstructural changes occurring during reduction.
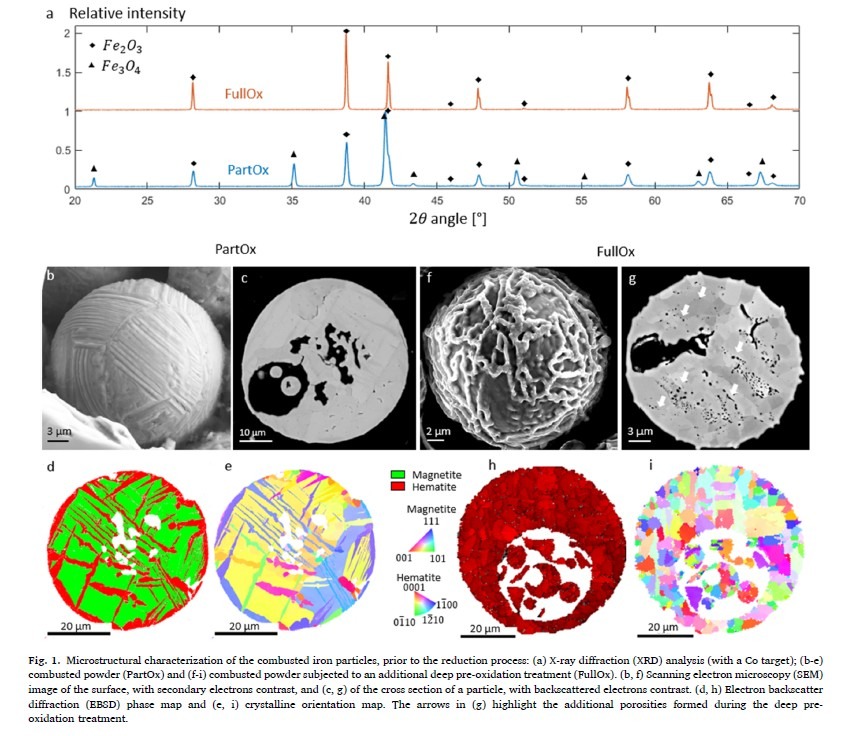
Experimental results showed the reduction process underwent significant phase transformations, starting with reduction of hematite to magnetite and eventually forming metallic iron. Pre-oxidized samples (FullOx) exhibited homogeneous reduction and finer microstructure compared to as-combusted samples (PartOx) which displayed heterogeneous phase distribution.
Deep pre-oxidation altered the reduction pathway, with FullOx demonstrating more uniform reduction across the sample attributed to pre-oxidation treatment creating uniform hematite phase which reduced to magnetite and iron more consistently. Temperature was critical for reduction rate, with higher temperatures enabling faster kinetics. Interestingly, total reduction time for pre-oxidized samples did not differ significantly from combusted samples at studied temperatures, though detailed analysis suggested nuanced pre-oxidation effect on kinetics of individual phase transformations within the process.
SEM and EDS revealed metallic iron nucleated predominantly around pores and grain boundaries in pre-oxidized samples, indicating active reduction sites, while combusted samples showed irregular pore distribution and microstructure due to mixed phase composition.
Conclusion
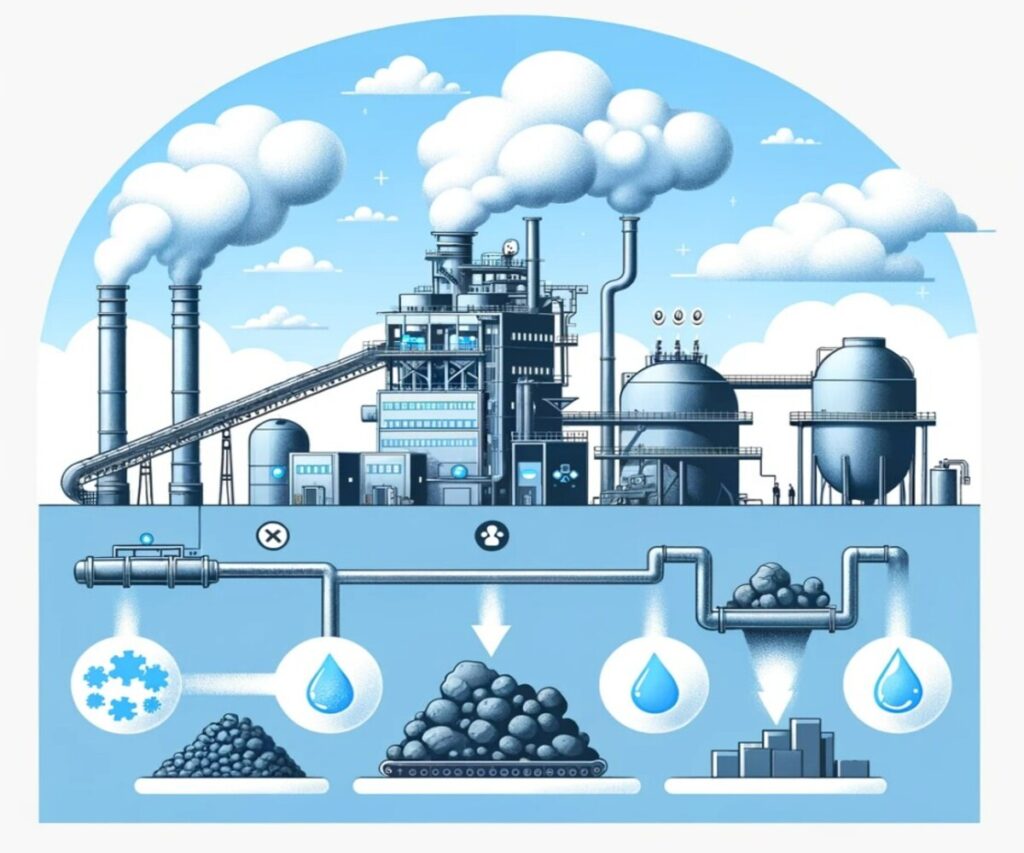
This comprehensive study sheds light on the hydrogen direct reduction (HyDR) of iron, particularly emphasizing the significant role of pre-oxidation and temperature in influencing the reduction kinetics and microstructural evolution. By meticulously examining the phase transitions and microstructural changes through advanced analytical techniques, the research advances our understanding of the HyDR process.
The insights garnered from pre-oxidized and combusted iron powder samples underscore the potential efficiencies that can be achieved in sustainable iron production, aligning with broader environmental objectives. Furthermore, the detailed exploration of reduction behaviors, from the influence of pre-oxidation to the critical role of temperature, contributes to optimizing the hydrogen direct reduction process for iron, paving the way for more sustainable practices in the iron and steel industry.
Source: Choisez, Laurine, et al. “Hydrogen-based direct reduction of combusted iron powder: deep pre-oxidation, reduction kinetics and microstructural analysis.” Acta Materialia (2024): 119752.
https://doi.org/10.1016/j.actamat.2024.119752
※ This report has been compiled for the purpose of providing general information. It is based on data gathered by CHEMiFORGE. Should you have any inquiries or need to make decisions based on this report, it is advisable to consult with a CHEMiFORGE.