Introduction : Technology of Change from Cabon dioxide to Acetic Acid
Acetic acid is a very important industrial chemical due to its high manufacturing capacity and diverse applications worldwide. Currently, acetic acid is mainly synthesized through carbonylation of methanol, where both reactants are derived from fossil fuels.
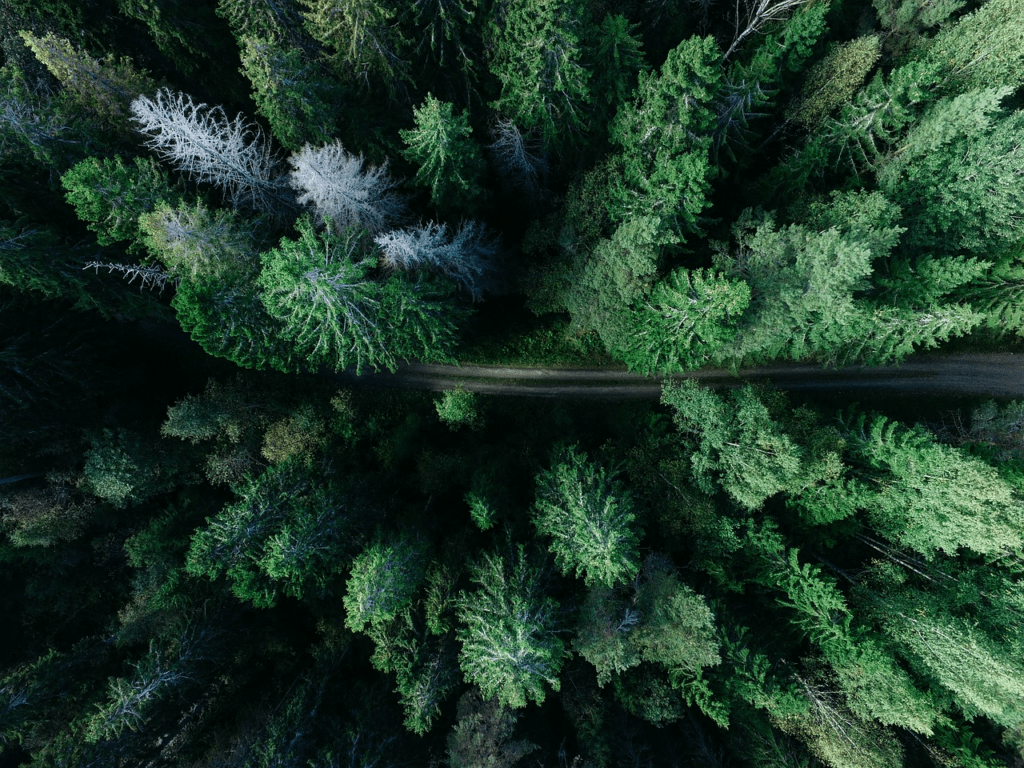
It is useful in utilizing carbon dioxide (CO2) to reduce carbon emissions, and converting carbon dioxide to acetic acid is a very desirable method to achieve carbon neutral emissions, but many challenges remain to achieve this efficiently.
Development of iron based MOF catalyst
Scientists from Australia, the United States, and Japan have proposed the thermally modified MIL-88B MOF (Metal Organic Framework) as a catalyst for highly selective production of acetic acid through methanol hydrogencarboxylation, and MIL-88B MOF combines iron and iron oxide. It has a double active site, and the catalyst showed high activity and stability.
The iron-based MIL-88B MOF catalyst was prepared using a wet impregnation method, which is a general method for introducing metal active sites into a solid catalyst. An iron-based MIL-88B MOF catalyst was prepared using a hydrothermal method, which synthesizes a material based on 10% iron and MIL-88B MOF by applying high temperature and pressure.
Then, an aqueous hydrocarboxylation reaction of methanol was performed using iron-based MIL-88B MOF as a catalyst and lithium iodide (LiI) as a co-catalyst.
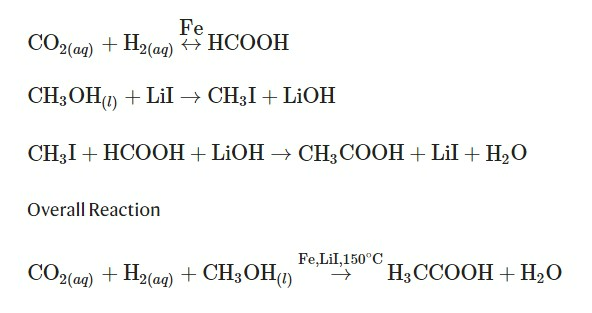
Methanol hydrocarboxylation for acetic acid production is a reaction that produces acetic acid and water by adding carbon dioxide, hydrogen, and methanol. Carbon dioxide and hydrogen are adsorbed on the iron-based MIL-88B-500 catalyst, and the adsorbed carbon dioxide and hydrogen are converted to formic acid. Formic acid is a precursor to acetic acid and is widely used in acetic acid production.
Methanol is converted to methyl iodide (CH3I) through reaction with lithium iodide (LiI), a cocatalyst, and reacts with formic acid to produce acetic acid, which is desorbed from the catalyst and the methyl iodide participating in the reaction is iodinated again. It is converted to lithium and participates in the reaction again.
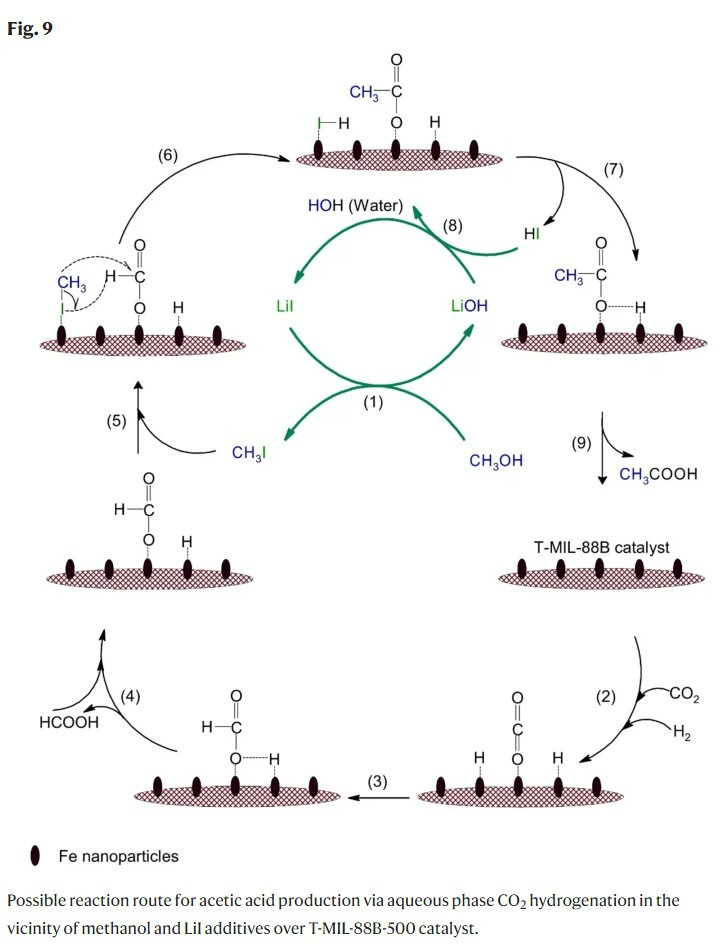
Conclusion
The development of a thermally modified iron-based metal-organic framework (MOF) catalyst has yielded promising results, exhibiting remarkable catalytic activity and stability for the conversion of aqueous carbon dioxide into acetic acid. This innovative catalyst holds significant potential for widespread application in the production of acetic acid via the formate pathway through the hydrocarboxylation of methanol using carbon dioxide as a feedstock. The ability of this catalyst to facilitate the transformation of a greenhouse gas into a valuable chemical product represents a significant stride towards the realization of a sustainable and circular economy.
Notably, this achievement constitutes a major milestone in the ongoing efforts to develop eco-friendly catalysts capable of converting carbon dioxide into commercially viable products. The iron-based MOF catalyst’s exceptional performance in promoting the selective formation of acetic acid from carbon dioxide and methanol underscores its potential to contribute significantly to the broader goal of achieving carbon neutrality through the valorization of carbon dioxide emissions.
The development of such catalytic systems is driven by the pressing need to mitigate the environmental impact of anthropogenic carbon dioxide emissions, which are widely recognized as a primary contributor to global climate change. By providing a viable pathway for the utilization of carbon dioxide as a renewable feedstock, this catalyst offers a promising solution to not only reduce net emissions but also to create value-added products from a previously waste stream.
Furthermore, the thermally modified iron-based MOF catalyst exhibits remarkable stability under the reaction conditions, ensuring consistent performance and minimizing the need for frequent catalyst regeneration or replacement. This attribute is particularly desirable from an industrial perspective, as it translates into reduced operational costs and downtime, thereby enhancing the economic viability of the process.
The successful demonstration of this catalyst’s capabilities represents a significant achievement in the development of an eco-friendly and sustainable approach to acetic acid production. Acetic acid is a versatile chemical intermediate with a wide range of applications in various industries, including the production of polymers, pharmaceuticals, and food additives. By providing a greener alternative to traditional fossil-fuel-based production methods, this catalyst could potentially contribute to the decarbonization of these industries and support the transition towards a more sustainable future.
Moreover, the advancements made in the development of this catalyst serve as a testament to the ongoing progress in the field of carbon dioxide utilization and the potential of MOFs as promising catalytic platforms. The unique structural and chemical properties of MOFs, combined with their inherent tunability, have opened up new avenues for the design and synthesis of highly efficient and selective catalysts tailored for specific applications.
As research efforts continue to build upon these significant achievements, it is expected that further breakthroughs will be made in the development of eco-friendly catalysts for the conversion of carbon dioxide into a diverse range of valuable products. These advancements will undoubtedly contribute to the overarching goal of achieving carbon neutral emissions, fostering a more sustainable and environmentally responsible approach to industrial processes and economic activities.
Ahmad, Waqar, et al. “Aqueous phase conversion of CO2 into acetic acid over thermally transformed MIL-88B catalyst.” Nature communications 14.1 (2023): 2821.
https://doi.org/10.1038/s41467-023-38506-5
※ This report has been compiled for the purpose of providing general information. It is based on data gathered by CHEMiFORGE. Should you have any inquiries or need to make decisions based on this report, it is advisable to consult with a CHEMiFORGE.